힘, 가속도, 압력의 측정
힘은 벡터를 가지고 있는 양이다. 이 벡터의 방향을 측정하여 발생하고 있는 위치나 힘의 전달방향/경로(TPA)를 측정할 수 있다.
힘(F)은 질량(m)과 가속도(a)의 곱으로 나타낼 수 있으므로 힘이 가해지는 질량을 이미 알고 있다면 가속도를 알 수 있다. 또한 힘은 압력(p)과 면적(A)과의 곱이므로 힘이 가해지는 집중 하중의 수직면적을 알고 있다면 힘을 가했을 때 압력 또한 알 수 있다.
그런데 똑같이 생긴 피에조(PIEZO)형식의 센서라도....
https://contents.premium.naver.com/bisope/visope/contents/240521072754024qb

힘이 먼저인가? 가속도가 먼저인가? ----------------------------------------------------------------------------------------------------------------------- 가속도센서의 원리를
contents.premium.naver.com
Coupling & Coupling effect
위에서 말한 설비의 각 기계 구성요소인 구동부(모터, 터빈, 내연기관)와 피동부(펌프, 팬, 압축기 등)를 연결해 주는 또 하나의 구성요소를 ‘커플링’이라고 한다. 이 커플링의 종류로는 직결플랜지, flexible, jaw, 고무, 기어, 벨트, 체인, 마그네틱 등이 있다. 이 단어는 기계를 조금만이라도 알고 있는 사람이라면....
https://contents.premium.naver.com/bisope/visope/contents/240523055937516yz

커플링과 커플링현상 (Coupling) -------------------------------------------------------------------------------------------------------------------------- 기계의 상
contents.premium.naver.com
DE, NDE와 Outboard, Inboard
설비의 위치를 호명하는 것은 전체설비의 진동평가가 최고 진동점의 값으로 이루어지기도 하며 비교대상의 위치와 구분이 필요할 때에도 거론되므로 이미 많은 부분 약속이 되어 있는 사항이다. 그러나 서로 다른 단어로 불러지기도 하는데 이를 정리하여...
https://contents.premium.naver.com/bisope/visope/contents/231123080239310pm

진동센서의 측정방향과 위치 (부하측, 반부하측) ------------------------------------------------------------------------------------- 'NDE측 Horizontal진동이 높다'고 합니다. 어느 위치
contents.premium.naver.com
물소리는 없다.
잘 생각해 보면, 사실 물소리는 없고 물로 인해 발생되는 소리는 있습니다.
물은 압력을 주어도 부피가 줄지 않는 비압축성유체입니다. 따라서 물에 압력을 가하면 압력이 약한 곳으로 터져 흐르며 부피당 질량이 있으므로 비중과 (‘비중’;물의 밀도와 비교하여 모든 물질을 표현함) 중력에 따라...
https://contents.premium.naver.com/bisope/visope/contents/240524080658725eg

생진소시리즈115- 물소리는 어디에서 발생하는가? 비가 오면 빗소리로 알아채고 변기를 내리면, 파도가 치면, 폭포에서도 물소리가 납니다. 졸졸졸… 때로는 콸콸콸… 종류도 다양한 이러한 물소리는 시원한 느낌도 있기는 하지만 소음으로 느낄 때도 있습니다. 엉뚱하지만 어디
contents.premium.naver.com
#유제기인소음, #유체진동, #밸브진동, #반부하측, #부하측, #커플링, #기어박스, #힘센서, #기어진동, #가속도센서, #진동센서, #피에조, #압전센서, #ICP, #IEPE, #진동교육, #진동문제, #진동모니터링
https://blog.naver.com/vs72
진동/소음/초음파음향방출/측정/결함원인분석/공학지식공유/건물진동소음/구조진동/회전기계/공진분석/고유주파수/FFT/설비진단/조기결함/주파수분석/방진방음/플랜트/공사장건설도로철도/계측장비센서/PDM,CBM,VMS,CMS/기계-구조-배관-건물-공사장-철도/모니터링시스템,MODAL/ODS/진동자격/기술자문/연구심의/교육강의/소음진동기술사/BISOPE/VISOPE,........ 프리미엄컨텐츠-> https://contents.premium.naver.com/bisope/visope
blog.naver.com
www.kcbm.kr
![[한국CBM-상태 진단모니터링 - 홈] 상태측정분석, 특성화 모니터링시스템, CBM진동교육.... CBM 종합솔루션...한국CBM](https://dthumb-phinf.pstatic.net/?src=%22https://modo-phinf.pstatic.net/20210819_272/16293274516652vtVY_JPEG/mosaK9BOCG.jpeg?type=f320_320%22&type=ff120)
측정분석(진동소음)기술컨설팅+CBM모니터링시스템+교육
www.kcbm.kr
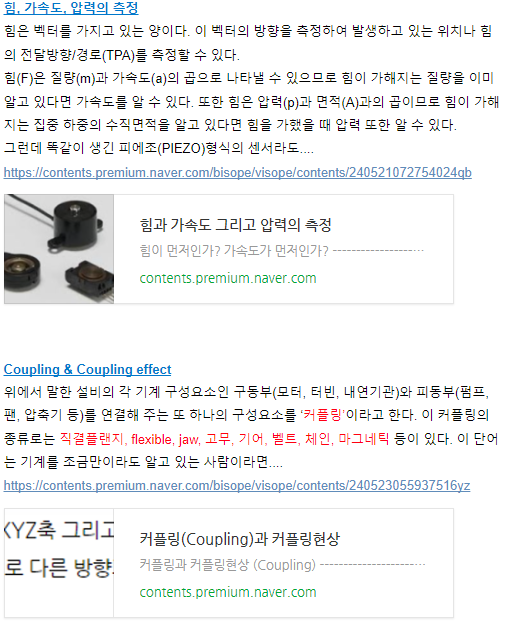
사진 설명을 입력하세요.